Porosity in Welding: Identifying Common Issues and Implementing Best Practices for Prevention
Porosity in welding is a prevalent concern that commonly goes unnoticed until it creates substantial troubles with the honesty of welds. In this conversation, we will certainly discover the key factors adding to porosity development, analyze its detrimental results on weld efficiency, and go over the finest methods that can be taken on to lessen porosity occurrence in welding procedures.
Typical Reasons of Porosity
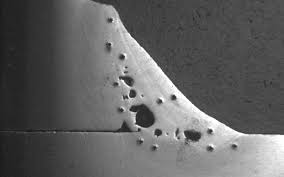
Utilizing unclean or wet filler materials can present pollutants right into the weld, adding to porosity issues. To reduce these typical reasons of porosity, thorough cleaning of base steels, correct shielding gas option, and adherence to optimum welding criteria are important methods in attaining high-quality, porosity-free welds.
Influence of Porosity on Weld Quality

The existence of porosity in welding can significantly compromise the structural honesty and mechanical residential or commercial properties of welded joints. Porosity creates voids within the weld steel, weakening its general stamina and load-bearing capability. These spaces serve as anxiety concentration points, making the weld much more prone to fracturing and failing under applied tons. Additionally, porosity can reduce the weld's resistance to corrosion and other environmental factors, further diminishing its long life and efficiency.
Welds with high porosity levels often tend to exhibit lower effect stamina and decreased capability to flaw plastically before fracturing. Porosity can hinder the weld's my review here capacity to successfully transmit pressures, leading to early weld failure and prospective safety and security risks in vital structures.
Finest Practices for Porosity Prevention
To enhance the architectural stability and top quality of welded joints, what particular procedures can be applied to decrease the event of porosity throughout the welding process? Using the appropriate welding strategy for the details product being bonded, such as changing the welding angle and gun position, can further prevent here porosity. Regular examination of welds and prompt removal of any type of issues identified throughout the welding procedure are vital methods to avoid porosity and produce premium welds.
Importance of Appropriate Welding Strategies
Executing appropriate welding methods is paramount in guaranteeing the architectural integrity and high quality of bonded joints, constructing upon the foundation of efficient porosity avoidance why not try this out measures. Extreme warmth can lead to increased porosity due to the entrapment of gases in the weld pool. In addition, using the appropriate welding parameters, such as voltage, present, and take a trip rate, is essential for accomplishing audio welds with minimal porosity.
In addition, the option of welding procedure, whether it be MIG, TIG, or stick welding, ought to align with the specific needs of the task to make sure optimal results. Appropriate cleansing and prep work of the base steel, along with choosing the appropriate filler product, are additionally important elements of skillful welding techniques. By adhering to these best methods, welders can lessen the threat of porosity development and generate high-quality, structurally audio welds.
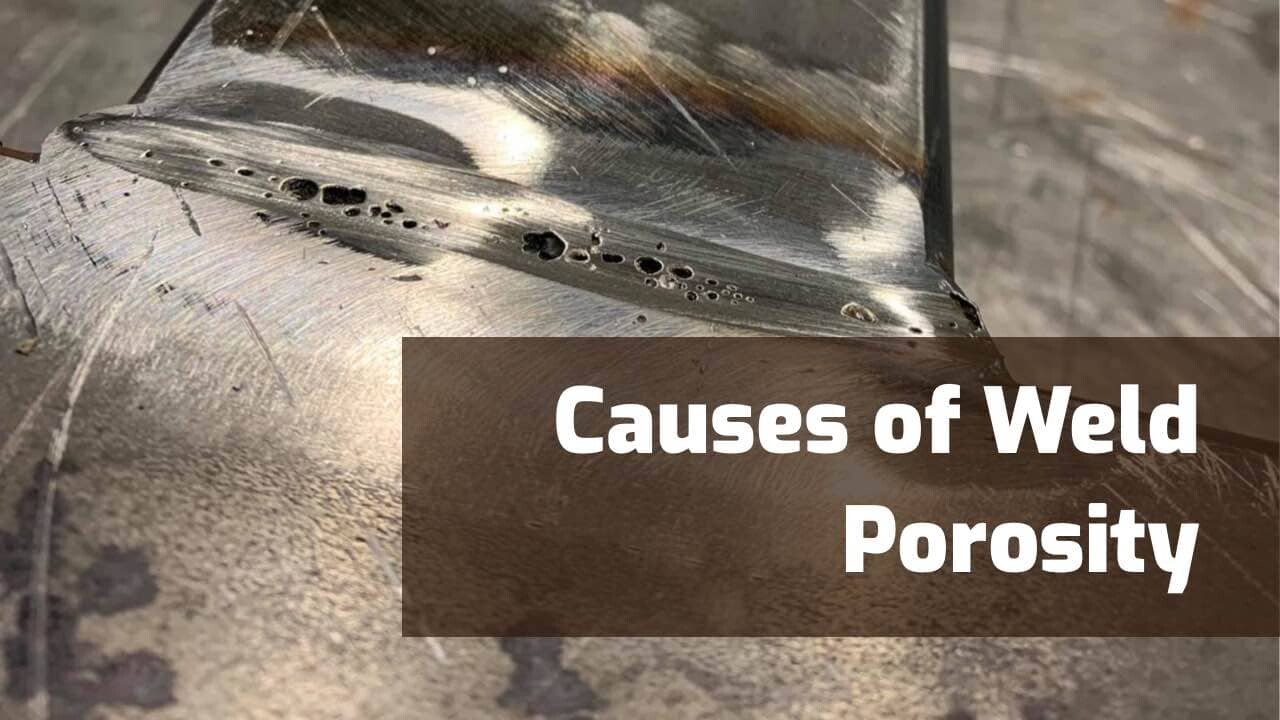
Checking and Quality Control Steps
Quality assurance actions play an important function in validating the honesty and integrity of bonded joints. Examining treatments are essential to discover and stop porosity in welding, ensuring the stamina and toughness of the last item. Non-destructive screening techniques such as ultrasonic testing, radiographic screening, and visual assessment are frequently utilized to determine prospective problems like porosity. These methods enable the analysis of weld quality without endangering the stability of the joint. What is Porosity.
Post-weld inspections, on the various other hand, analyze the final weld for any type of problems, including porosity, and validate that it fulfills defined requirements. Executing a comprehensive high quality control strategy that consists of comprehensive screening procedures and examinations is vital to decreasing porosity issues and making certain the overall quality of bonded joints.
Final Thought
To conclude, porosity in welding can be an usual concern that impacts the quality of welds. By determining the typical root causes of porosity and applying ideal practices for prevention, such as proper welding techniques and testing steps, welders can make sure excellent quality and trusted welds. It is vital to prioritize prevention methods to reduce the incident of porosity and preserve the stability of welded structures.
Comments on “Comprehensive Guide: What is Porosity in Welding and How to avoid It”